Jagtap is India’s leading manufacturer of Welded Wedge Bar Screen Drums for Rotary Screen Units. They are well known in the industry for their superior construction, high durability and quality with a proven record. Wedge Bar Screen Drums are a vital part of Rotary Screens used in the Sugar Industry for raw Sugarcane juice filtration.
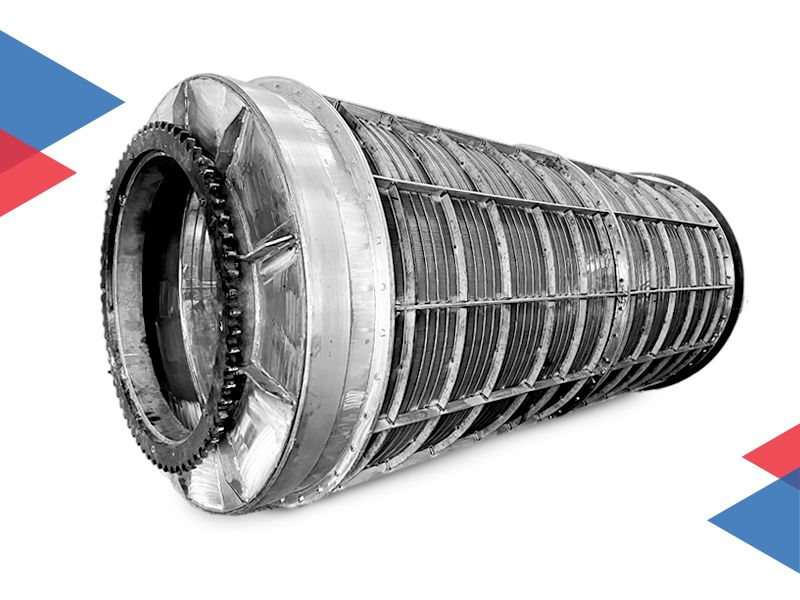
- Ready to fit Screen Drums Assembly for effective retrofitting for major OEMs make Rotary
- 3500+ nos of Jagtap Welded Wedge Bar Screen Drums Successfully operating in sugar mills globally
Jagtap’s micro-fine rotary drum screen unit for secondary/hot raw juice & clarified juice filtration. Our exclusive Micro Fine Rotary Drum Screens are precision-fabricated Laser Welded Screen, enabling us to provide filtration ratings as fine as 20 microns.
Jagtap’s Micron Fine Rotary Screen Units can be used for fine filtration at various stages of Juice Filtration, from Primary Raw Juice to Clarified Juice.
As per the recent trend and proven filtration methodology the Secondary Rotary Screen Unit with 250 microns followed by 150 microns Rotary Screen Unit for Raw Hot Juice and further Clarified juice is also filtered through the Rotary Screen unit to achieve the highest quality of clear juice without suspended matter, which in turn is necessary for good sugar quality.
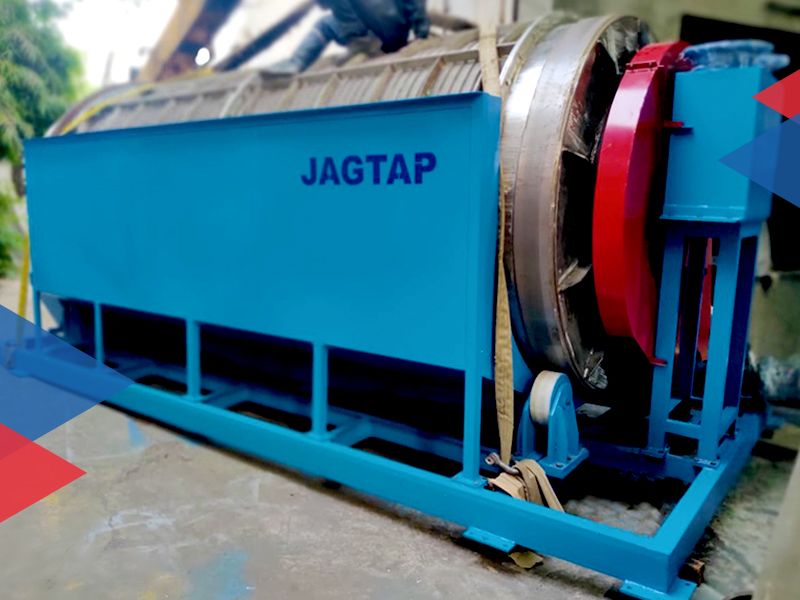
“High-Performance Way of Removing Suspended Solids from Liquids” This “Jagtap” principle introduces liquid under minimum headloss conditions and rotates the screen in the opposite direction so that maximum shear velocity is achieved. This is used for fast separation of solids from liquid. This principle not only carries the operation at a reduced cost but also increases substantially the quantity of raw juice handled on a specific screen size. Screening efficiency is also improved as, in all cases, the raw juice is introduced tangentially onto the contra-rotating face. Because of the shallow approach, this system also increases the percentage of Bagacillo capture off the screen surface. Drums rotating in the same direction as that of the juice flow cause flooding of the juice adversely affecting screening efficiency.
While mounting the screen, a fine gradient is provided towards the discharge end. The gradient is kept to a minimum to allow an increased retention period. While a higher percentage of juice recovery is assured in this arrangement, it also helps improve. drying of bagacillo to some
- Internally-fed Rotary Screen uses a cylindrical drum mounted on a trunnion holding plate that is supported on 2 pedestal bearing blocks
- The discharge end of the drum rests on two sets of self-aligning twin rollers
- The rotating screen is a unique metal-to-metal welded wedge bar screen with an aperture size ranging from 0.2 to 0.7mm and also as per customer requirements
- Rotary screen sizes range from 1000 mm to 2400 mm ID and length from 100 mm to 5600 mm. Flow rates are dependent on the Rotary Screen’s open area and size.
Method of Operation
Raw juice enters a collection/diversion box, which extends 2/3 the length of the drum, where the flow is evenly distributed onto the sidewalls of the drum. Solids are retained on the rotary screen surface as the liquid flows by gravity through the rotating screen openings.
Splashguards direct the raw juice to a central drainage area, and the solids are transported axially, assisted by a gradient to the open end of the drum. The drum rotation allows the entire screening surface to be continuously or intermittently washed by a fixed external spray bar fitted with a bank of spray nozzles, orated by a solenoid valve with a timer control panel.
In most of the existing Rotary Screen units, the Feed end shell and Discharge shell assembly move on a single contact roller and thrust roller through a sprocket-chain drive. In a few other cases, rotation of the screen is achieved with spindle assembly assisted by single Bearing/Pedestal assembly. Both these systems generate more load on the screen reducing its file expectancy. Jagtap has, to improve this, introduced a unique spindle assembly with 2 Nos. self-aligned double-row Spherical Bearings with ‘masta’ pedestals on the drive end and the discharge end of the drum resting on two sets of self-aligned twin rollers. Since the bearing block, as well as roller assemblies, are self-aligning, the load generated on the screen is considerably reduced, ensuring high life expectancy. All bearings are self-aligned. This fact makes the bearings absorb any eccentricity/ovality in the assembly, ensuring a smooth drive and giving more life to the screen as well as the drive.